Traba Enables Growth for a Rural Manufacturer
Traba Enables Growth for a Rural Manufacturer
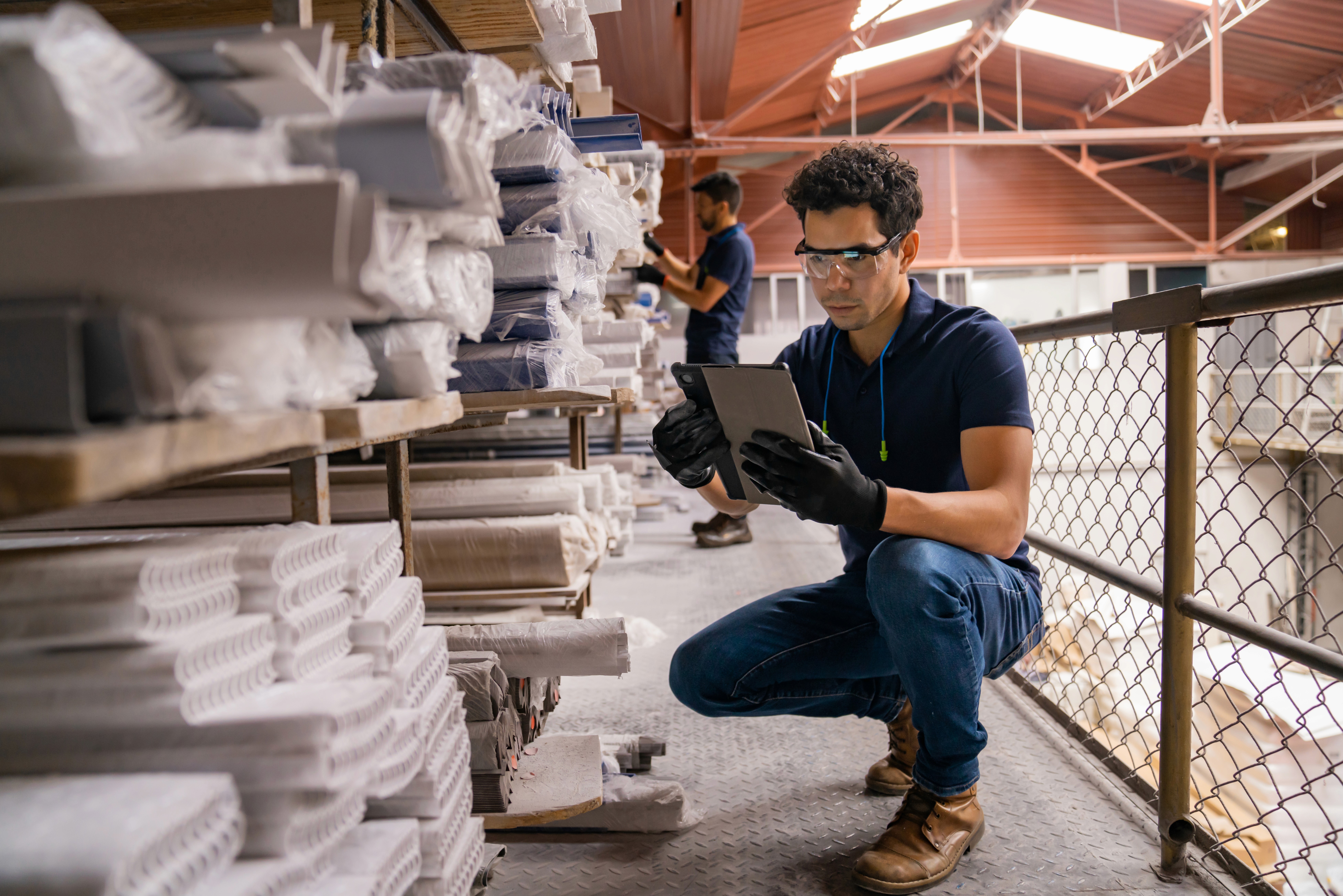
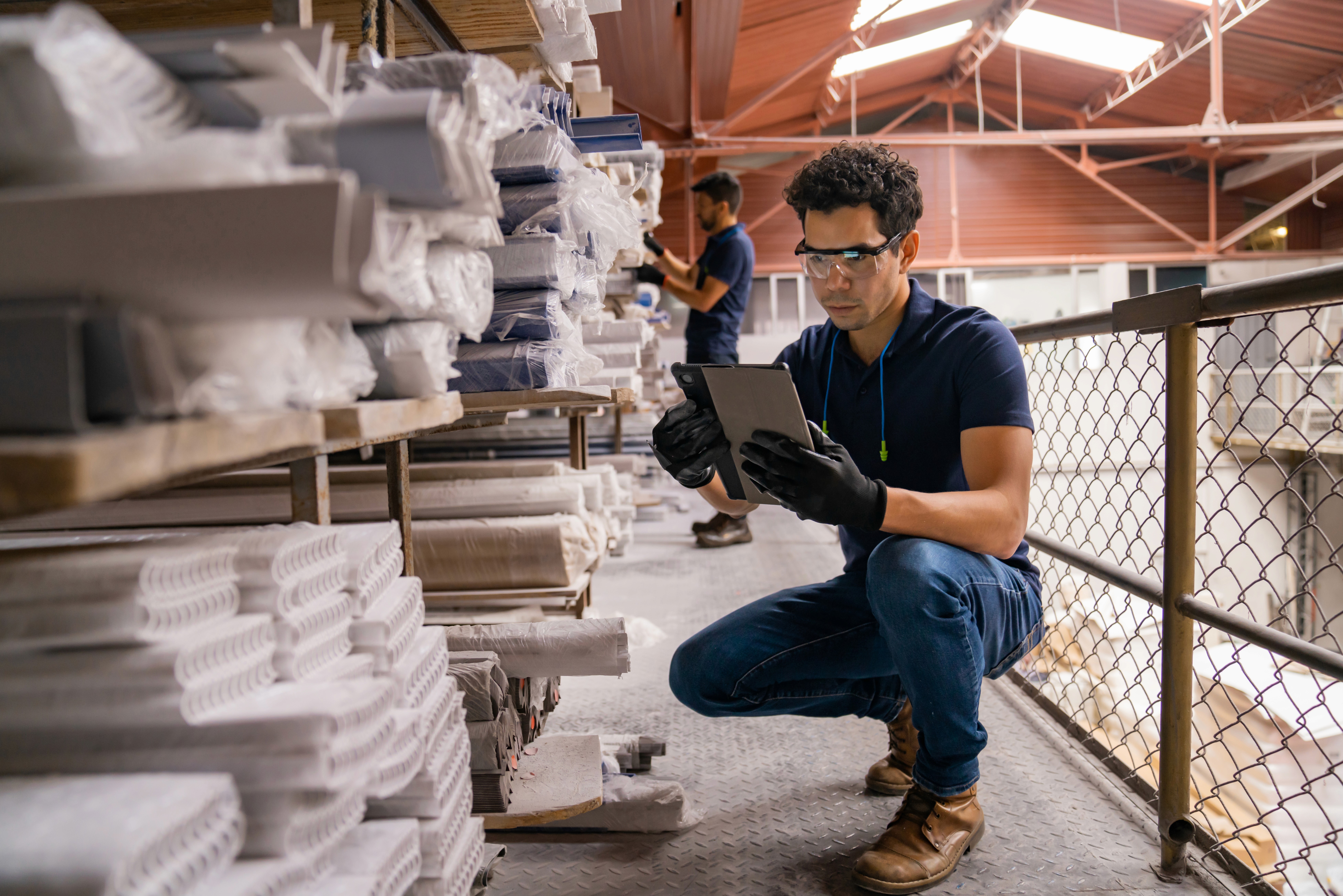
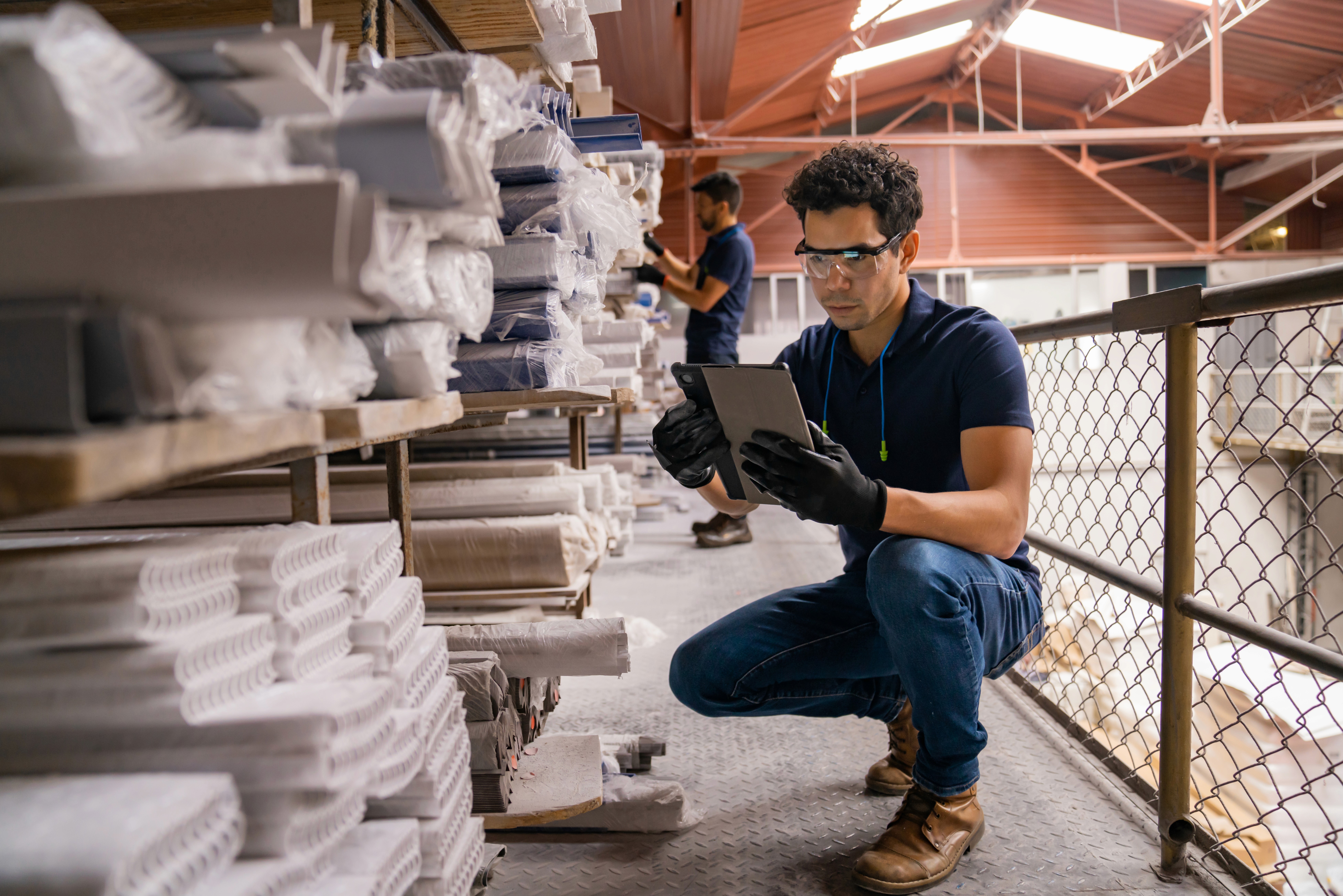
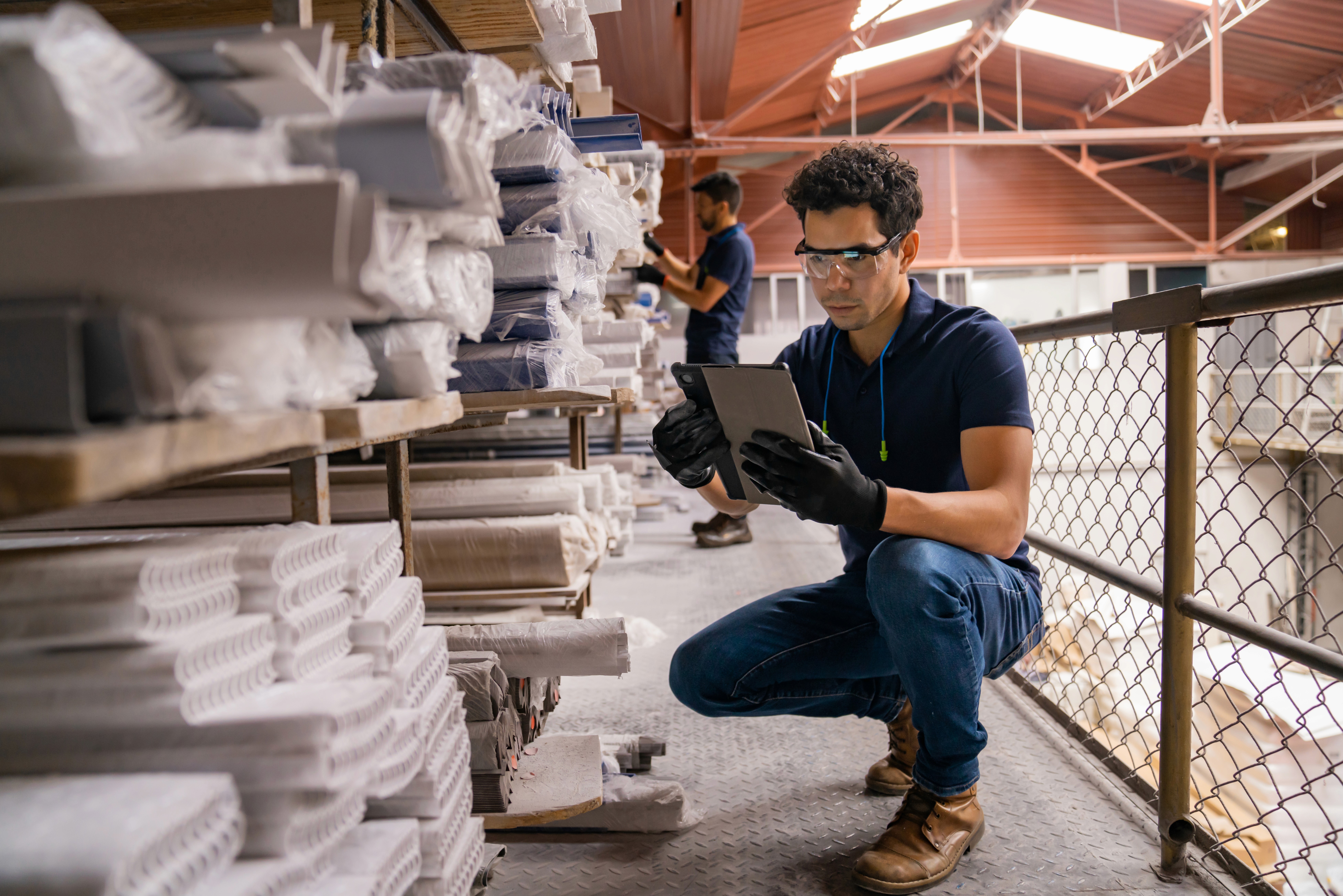
Traba
Dec 10, 2024
Introduction
Region: Central USA
Industry: Food Production
Roles: Machine Operators, Sheet Metal Workers, Material Handlers
Faced with chronic staffing shortages and production delays, a manufacturer of metal shelves for grocery retailers turned to Traba to tackle the challenges their previous agencies couldn’t solve. Located 60 miles from the nearest metropolitan area, the facility struggled to find reliable workers for critical roles, including machine operators and sheet metal workers
Problem
Our client, a manufacturer of metal shelves for grocery retailers, struggled to find reliable staffing to keep up with growing production demands. Despite its size, the 50,000-square-foot facility was understaffed in key final assembly roles such as machine operators and sheet metal workers. Filling these positions on the second shift proved challenging for their previous agencies which struggled to meet fill rates and routinely sourced workers with failed background experiences. Contributing to this challenge was our client’s location–the facility is 60 miles from the nearest metropolitan area.
Facing production delays, a chronic staffing shortage, and limited success with traditional solutions, the company turned to Traba to produce a high-quality light industrial workforce.
Solution
Given our client’s staffing challenges and low-tech operational structure, Traba took a tailored approach to deliver high-quality workers to their remote location. Traba’s team worked closely with HR and Operations leaders at the facility to better understand the operational challenges. Our team discovered that managers were hesitant to adopt new technology such as our mobile clock-in / clock-out system. They also uncovered that previous agencies had only sourced workers from nearby towns within a less than 5 mile radius. Traba’s team developed a better sourcing plan to find workers that were willing to make the trip from the outskirts of the metropolitan area by utilizing our digital recruitment platform. We also resolved the HR and Operations leaders’ hesitancy to adopt technology by installing a kiosk for workers to clock in and out, which minimized confusion and created a more seamless timekeeping experience with their existing operations.
Traba’s multi-channel recruitment strategy and thorough screening process ensured all candidates were fully aware of the requirements of the role and the specifics about the location. Our four point vetting process ensured the workers had aligned expectations and were prepared before arriving at the facility. By addressing potential issues early in the process, such as background check failures, Traba minimized the risk of turnover which mitigated retraining costs and ensured higher productivity for the contingent workforce.
The Results
Traba's labor solution quickly improved the company's ability to meet production demands. Traba proved valuable to the manufacturer by delivering on the initial requisition of five workers. After a successful first week, our client asked us to provide an additional 25 qualified candidates to maintain production amid surging demand. 93% of hires were considered a “successful match” and invited back for the following shift.This led to a streamlined onboarding process which led to ramping up production without any delays.
The powerful combination of sophisticated technology and a deep understanding of the company’s operational needs led to Traba succeeding where previous agencies struggled. The company’s second shift, which was historically understaffed and caused production delays, was now fully staffed with reliable workers who quickly integrated into the broader team. The tailored approach filled critical positions and ensured the workers were a good fit for the company’s long-term needs.
Introduction
Region: Central USA
Industry: Food Production
Roles: Machine Operators, Sheet Metal Workers, Material Handlers
Faced with chronic staffing shortages and production delays, a manufacturer of metal shelves for grocery retailers turned to Traba to tackle the challenges their previous agencies couldn’t solve. Located 60 miles from the nearest metropolitan area, the facility struggled to find reliable workers for critical roles, including machine operators and sheet metal workers
Problem
Our client, a manufacturer of metal shelves for grocery retailers, struggled to find reliable staffing to keep up with growing production demands. Despite its size, the 50,000-square-foot facility was understaffed in key final assembly roles such as machine operators and sheet metal workers. Filling these positions on the second shift proved challenging for their previous agencies which struggled to meet fill rates and routinely sourced workers with failed background experiences. Contributing to this challenge was our client’s location–the facility is 60 miles from the nearest metropolitan area.
Facing production delays, a chronic staffing shortage, and limited success with traditional solutions, the company turned to Traba to produce a high-quality light industrial workforce.
Solution
Given our client’s staffing challenges and low-tech operational structure, Traba took a tailored approach to deliver high-quality workers to their remote location. Traba’s team worked closely with HR and Operations leaders at the facility to better understand the operational challenges. Our team discovered that managers were hesitant to adopt new technology such as our mobile clock-in / clock-out system. They also uncovered that previous agencies had only sourced workers from nearby towns within a less than 5 mile radius. Traba’s team developed a better sourcing plan to find workers that were willing to make the trip from the outskirts of the metropolitan area by utilizing our digital recruitment platform. We also resolved the HR and Operations leaders’ hesitancy to adopt technology by installing a kiosk for workers to clock in and out, which minimized confusion and created a more seamless timekeeping experience with their existing operations.
Traba’s multi-channel recruitment strategy and thorough screening process ensured all candidates were fully aware of the requirements of the role and the specifics about the location. Our four point vetting process ensured the workers had aligned expectations and were prepared before arriving at the facility. By addressing potential issues early in the process, such as background check failures, Traba minimized the risk of turnover which mitigated retraining costs and ensured higher productivity for the contingent workforce.
The Results
Traba's labor solution quickly improved the company's ability to meet production demands. Traba proved valuable to the manufacturer by delivering on the initial requisition of five workers. After a successful first week, our client asked us to provide an additional 25 qualified candidates to maintain production amid surging demand. 93% of hires were considered a “successful match” and invited back for the following shift.This led to a streamlined onboarding process which led to ramping up production without any delays.
The powerful combination of sophisticated technology and a deep understanding of the company’s operational needs led to Traba succeeding where previous agencies struggled. The company’s second shift, which was historically understaffed and caused production delays, was now fully staffed with reliable workers who quickly integrated into the broader team. The tailored approach filled critical positions and ensured the workers were a good fit for the company’s long-term needs.
Read more articles
Maximize your facility's productivity
See exactly how all your staffing headaches will be solved by our industry experts today.
Maximize your facility's productivity
See exactly how all your staffing headaches will be solved by our industry experts today.
Copyright © 2024 All Rights Reserved by Traba
Copyright © 2024 All Rights Reserved by Traba
Copyright © 2024 All Rights Reserved by Traba
Copyright © 2024 All Rights Reserved by Traba