Think overtime is just about bumping up wages for your most reliable workers? Think again. In light industrial facilities, it's disproportionately hurting margins and efficiency.
Many operations managers cling to overtime as a safety net, especially during peak season when demand is at its highest. It's a familiar devil: predictable in its unpredictability. But this approach is similar to using a band-aid to treat a compound fracture. It might stem the immediate bleeding, but it does nothing to address underlying structural issues.
Despite the drawbacks, many operations leaders resort to overtime for one reason: the illusion of control. With overtime, managers know exactly who's on the floor. They're intimately familiar with each worker's strengths, weaknesses, and quirks. This workforce is a known quantity, an already-oiled machine that can be pushed to meet any demand spike.
Managers can predict with near certainty that John from the day shift will stay late to cover the evening rush, or that Sarah can handle the intricate packaging for the new product line. It's a comfort zone that feels safe, even as it slowly erodes productivity and morale.
According to the U.S. Bureau of Labor Statistics, the average overtime worked by a manufacturing employee was 3.6 hours/week during October 2023. A survey of overtime practices at American facilities found that some employees average up to 500 hours of overtime per year.
Light industrial facilities are chronically understaffed by anywhere from 10-25% as of October 2023, with material handlers and forklift drivers representing the most significant labor gaps at 34% and 31%, respectively. While operations managers and HR professionals are often aware of this staffing deficit, many maintain a lean workforce out of fear that demand could fall at the drop of a hat.
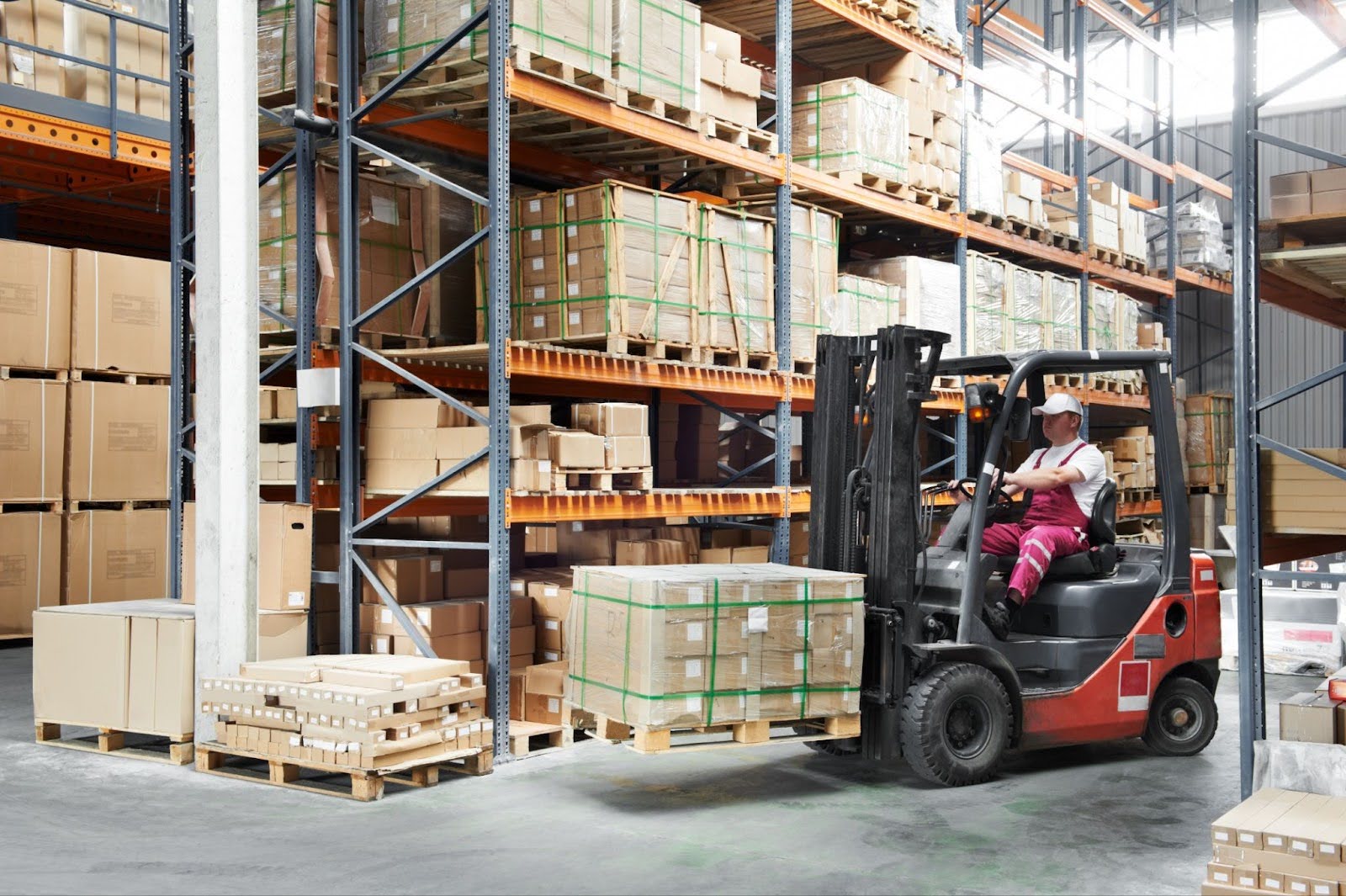
In response to this tightrope walk, many facilities default to overtime as a "set it and forget it" approach that is far from the fall-back it might appear to be.
Let's break it down:
1. Increased Error Rates: Workers in jobs with overtime schedules have a 61% higher injury rate compared to those without overtime. This elevated risk is attributed to the extended hours reducing alertness and increasing the likelihood of accidents. (BMJ Occ Med) (IOGP).
2. Burnout and Turnover: Employees working overtime are more susceptible to burnout. According to Gallup, employees who experience burnout are 2.6 times more likely to seek new employment opportunities. (BMJ Occ Med).
3. Compliance Risks: Mismanaged overtime can lead to wage and hour violations, with the average settlement for such lawsuits reaching $6.3 million in 2023. (NERA Economic Consulting, 2024)
When faced with the need to look past overtime and supplement their workforce, many leaders turn to traditional staffing agencies only to find themselves trading one problem for another. The typical agency model is akin to a black box: you submit a request, and workers appear. But who are these workers? What are their skills? Their work ethic? Their reliability? You’re not familiar with them in the same way that you are with John’s quirks or Sarah’s uncanny packing ability.
Last year, as John and Sarah’s plant manager, you relied heavily on overtime to gear up for the holiday rush. John clocked in for the day shift and often stayed until midnight, while Sarah was working weekends to keep up with demand. By the end of the season, John was exhausted, and Sarah hinted at looking for less demanding work.
This year, you face the same challenge, but you’ve learned from experience. Instead of overburdening your existing staff, you’ve explored more flexible staffing solutions that maintain productivity without sacrificing your employees' well-being.
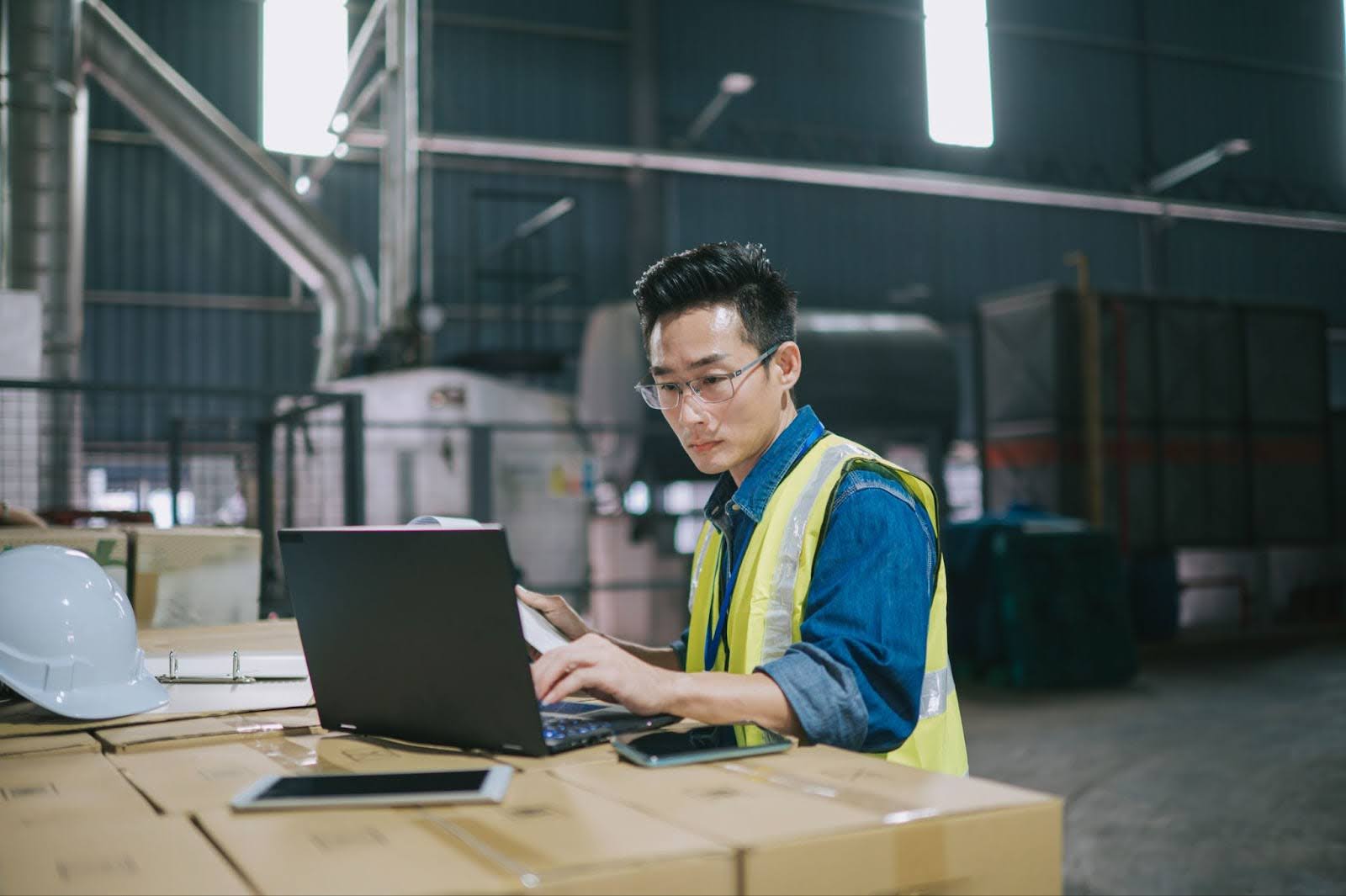
As the holiday season approaches, integrating additional team members becomes part of your strategy. Minimizing training time is key, so having workers with relevant experience who can quickly adapt to your facility’s specific needs is vital. Ensuring these workers are reliable, live nearby, and fit well within your company culture can significantly improve the overall efficiency of your operations.
The results of this approach can be immediate and tangible. With the right support, productivity remains high, error rates drop, and the morale of your core team improves. John and Sarah are still your go-to experts, but now they have the support they need to handle peak times without burning out. John can focus on overseeing quality control, while Sarah trains the new workers on unique packing requirements. The operation runs smoothly, orders go out on time, and the team feels like a well-oiled machine.
The businesses that will thrive in the coming quarter are those that view their workforce not as a fixed asset but as a dynamic, adaptable resource. Leveraging flexible staffing solutions not just as a temporary fix but as a strategic tool can help build a more responsive, efficient, and innovative operation.
Key Takeaways:
Illusion of Control: Overtime may give managers a sense of control by relying on familiar workers, but this approach brings hidden costs such as higher error rates, compliance risk, and reduced long-term productivity.
Efficiency Through Fit: Integrating temporary workers who have relevant experience and fit well within the company culture can allow an operation to fully capitalize on peak-season demand.
Long-Term Impact of Staffing Choices: The way you manage staffing during peak times can have lasting effects on employee morale, retention, and the overall success of your operations.