Introduction
Location: Austin, TX
Industry: Cosmetics Manufacturing
Roles: Production operators such as; packers, general labor and machine operators.
Our client is a family-owned business that specializes in producing organic and natural cosmetic products. Quality and precision are paramount to them, as they cater to clients who expect their orders to be meticulously fulfilled according to exact specifications. Their demand remains relatively steady throughout the year, with a peak during the summer months.
Our client prides themselves on long-standing relationships with their partners, largely attributed to their unwavering commitment to quality.
Problem
Previous staffing solutions failed to meet Good Manufacturing Practice (GMP) standards and communication needs of the business.
Our client faced significant challenges with their previous staffing agency. Workers often arrived unprepared for GMP requirements, such as having long nails or wearing wigs, which compromised product quality and safety. Additionally, there was a lack of clear role matching and poor communication between the business and their prior traditional staffing agency, resulting in unresolved issues and operational inefficiencies.
Before partnering with Traba, our client struggled with inconsistent labor quality and unreliable staffing solutions, particularly during their peak season. Their product quality suffered and they were at risk of losing customers. Their defect rate started to increase as their quality assurance team started to notice smeared labels. They needed a dependable workforce that could maintain high standards and effectively manage the increased demand.
Solution
Traba provided our client with a roster of pre-vetted, high-quality workers who were well-prepared to meet GMP standards and other operational requirements. On average, it takes our client 26 minutes to see their first sign up on shifts, with 83% of positions being filled 24 hours in advance of the shift start time.
Workers were required to complete GMP training and certification prior to accepting any roles. By utilizing Traba's console, our client could create customized rosters featuring their favorite workers, ensuring a consistent and reliable team. The block feature in Traba's system allowed the business to curate an ideal workforce that aligned with their specific needs, with 90% of their slots being filled by returning workers.
Results
Since partnering with Traba, our client has experienced significant improvements in workforce quality and operational efficiency. Traba was able to achieve a 99.6% fill rate across roles. (Fill rate is calculated using the number of workers that completed shifts divided by the number of workers initially requested.) Their defect rate and return rates have decreased. Traba's understanding of the cosmetic manufacturing industry and proactive approach has provided consistent and high-performing labor which allowed the business to meet their production targets without fail. The majority of their workers are sourced solely from Traba, especially during their peak season. Clear communication and support have been crucial in addressing issues promptly and maintaining smooth operations.
The ease-of-use of Traba's business portal enabled quick adoption for all members of their team. This has empowered our client to manage the day-to-day of their family-run facility effectively, leading to increased volume output and operational scalability. As their production lines expanded, Traba scaled with them, providing the necessary resources to support their growth.
Now, early discussions are underway about acquiring another facility, highlighting the potential for further business growth when partnering with Traba.
96%
96%
Fill Rate
Fill Rate
87%
87%
Worker Hire Rate
Worker Hire Rate
95%
95%
Workforce Consistency
Workforce Consistency
Read more success stories like this
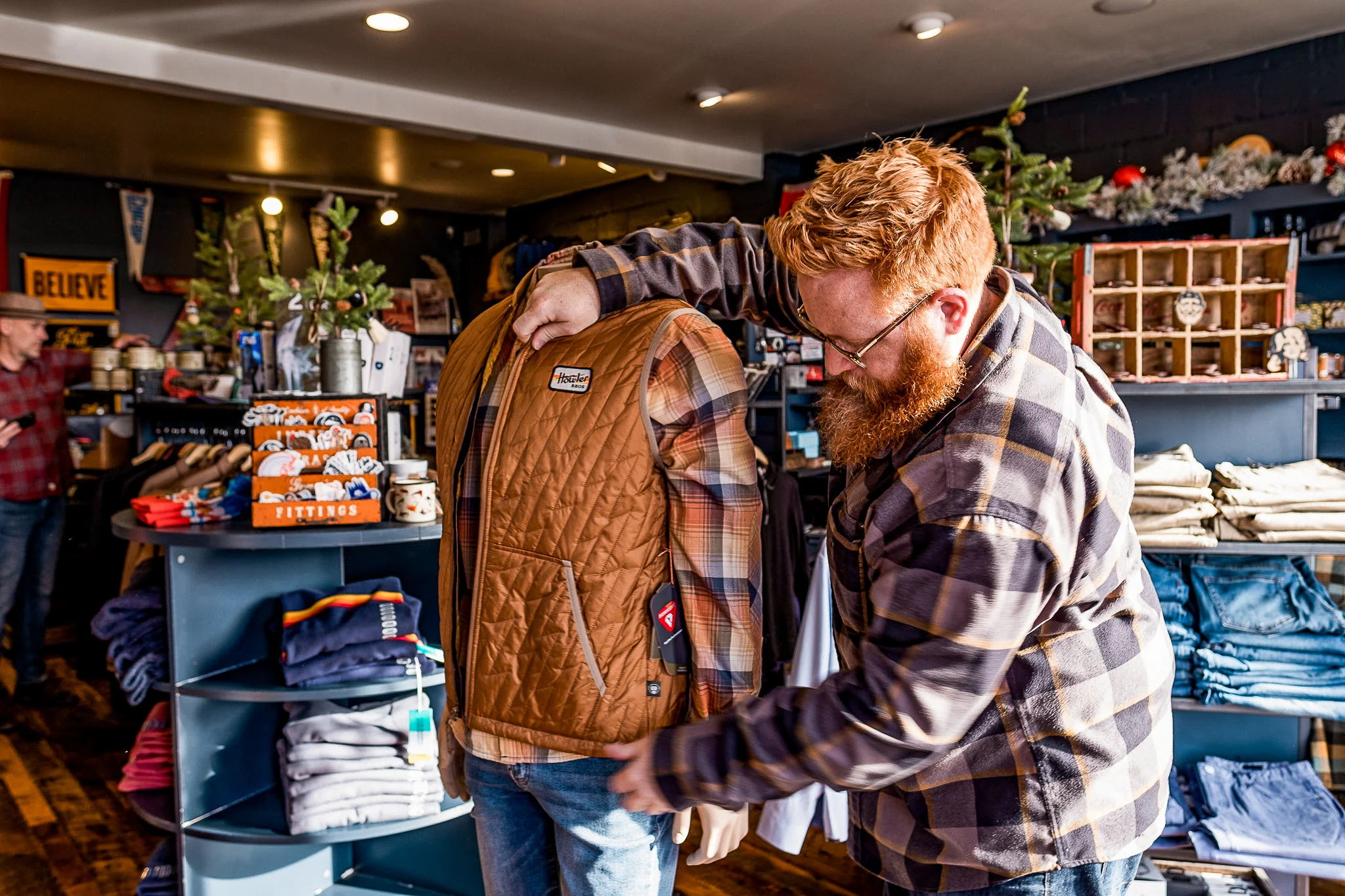
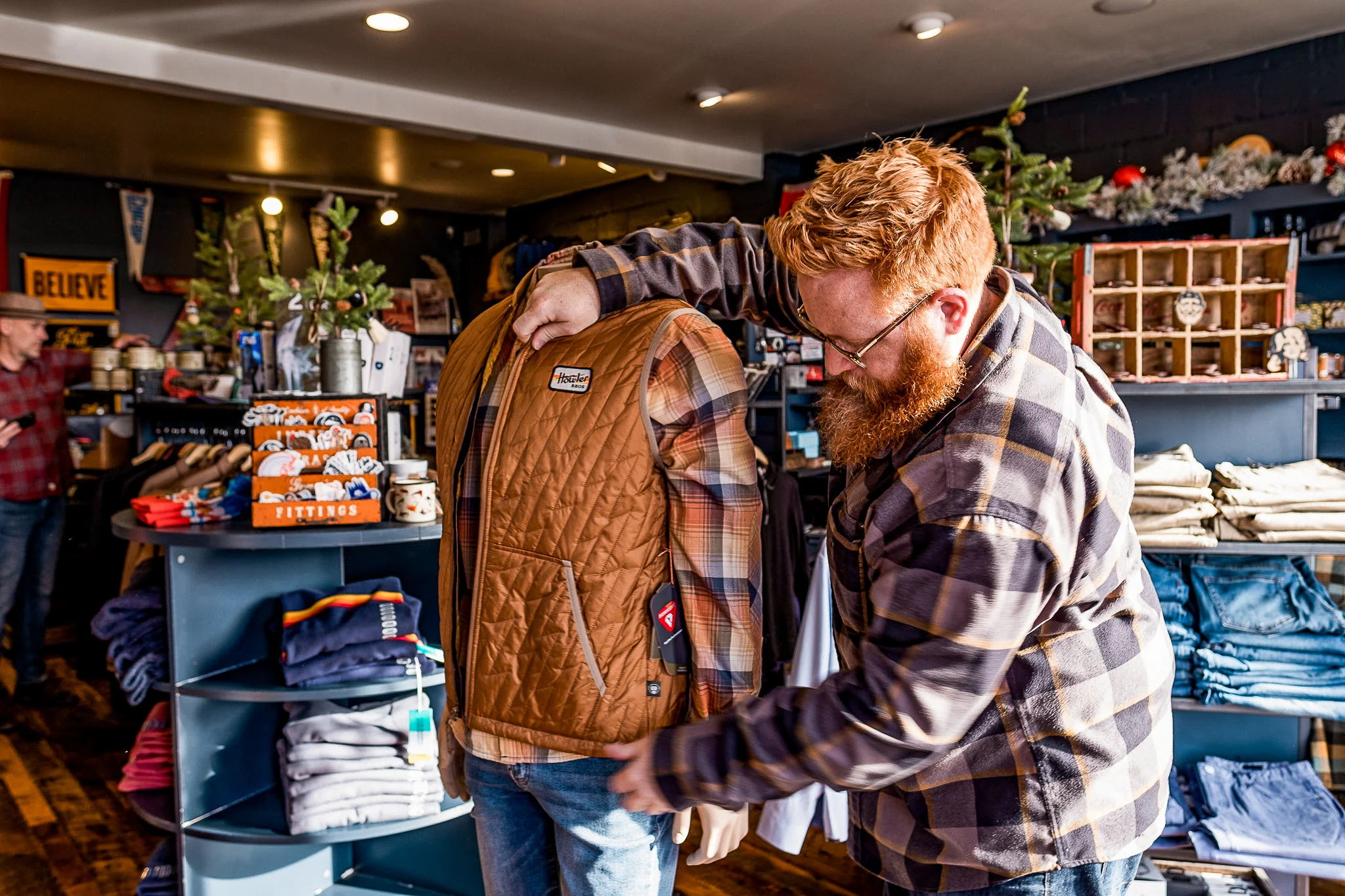
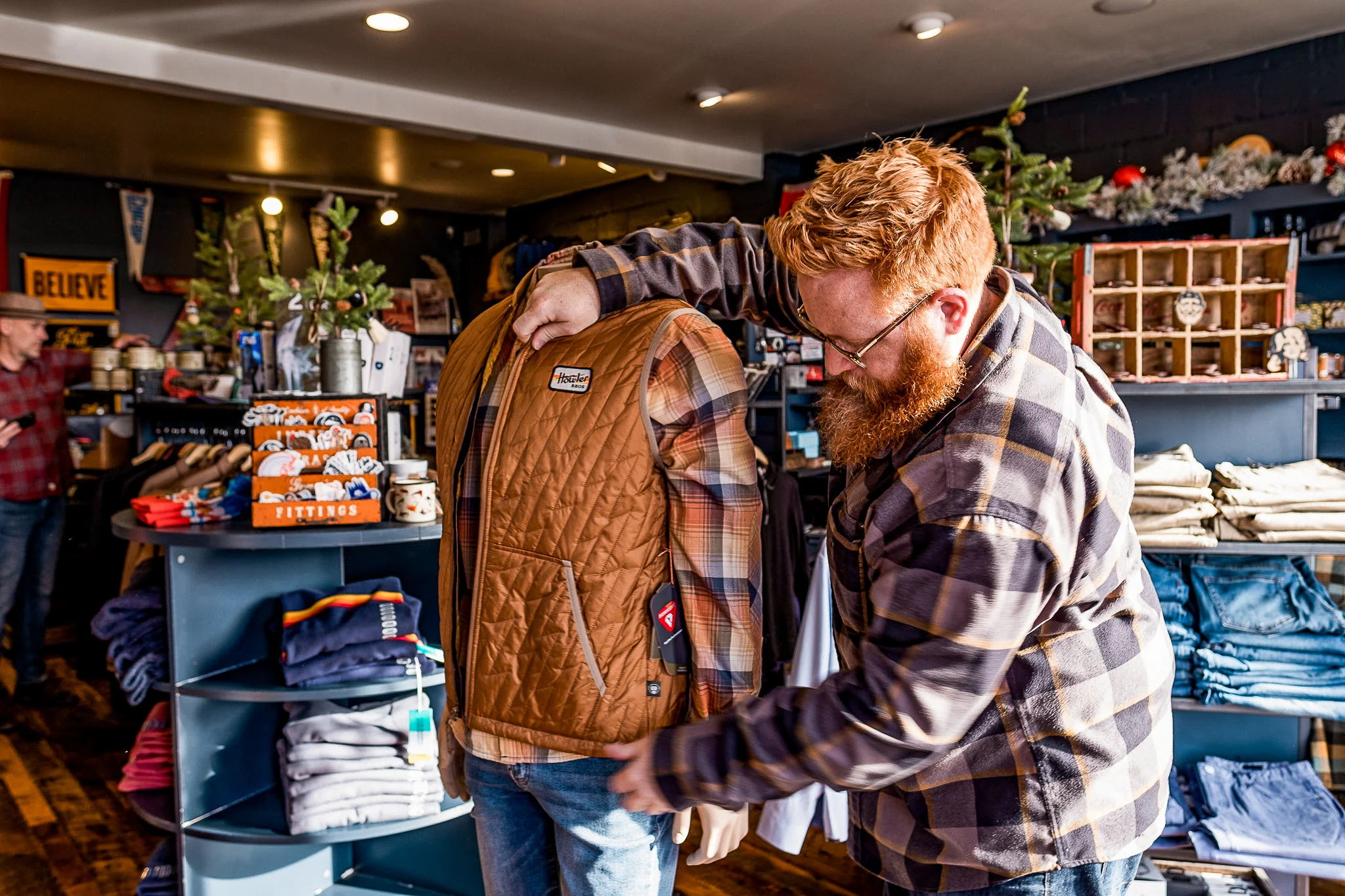
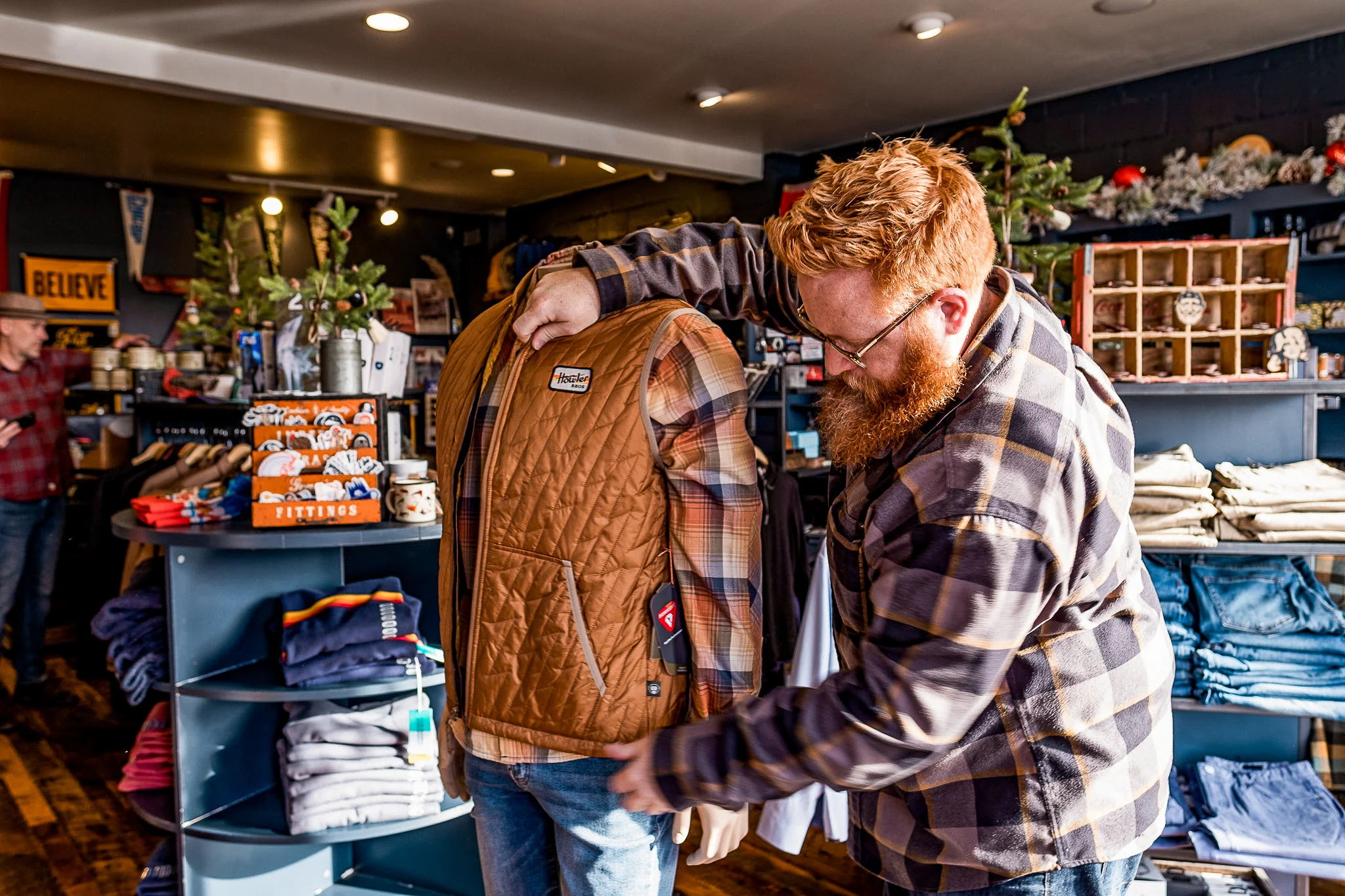
Fulfillment
Fulfillment
Fulfillment
Fulfillment
Apparel Brand Boosts Productivity by 200%
Apparel Brand Boosts Productivity by 200%
Apparel Brand Boosts Productivity by 200%
Our client, a Texas-based apparel company, faced a major backlog of 8,000+ e-commerce orders due to a strained 3PL during the holiday season. Traba quickly responded, filling the gaps by providing quality fulfillment workers within 24 hours. Over two weeks, Traba helped them clear the backlog, maintaining a 100% fill rate and operational excellence.
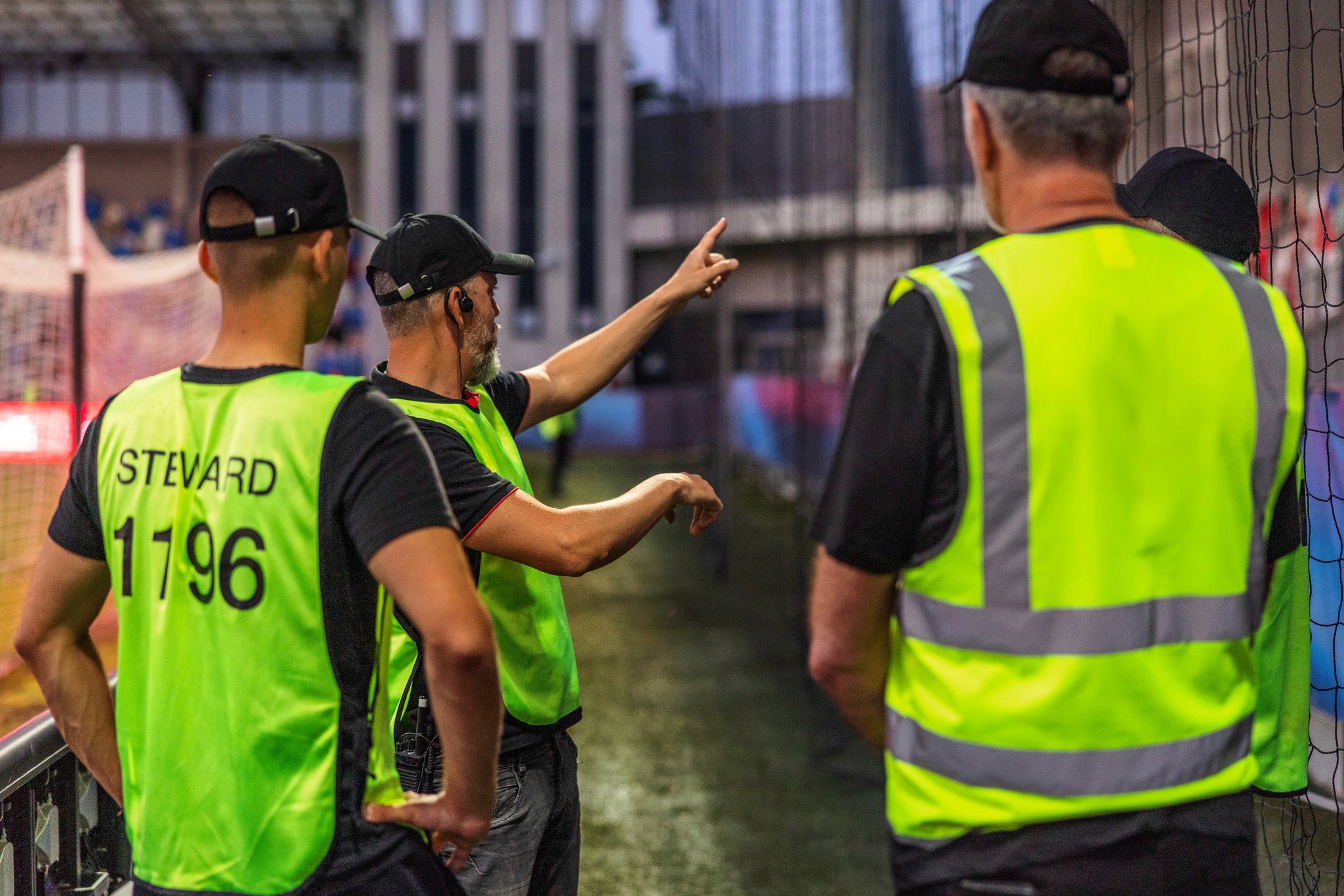
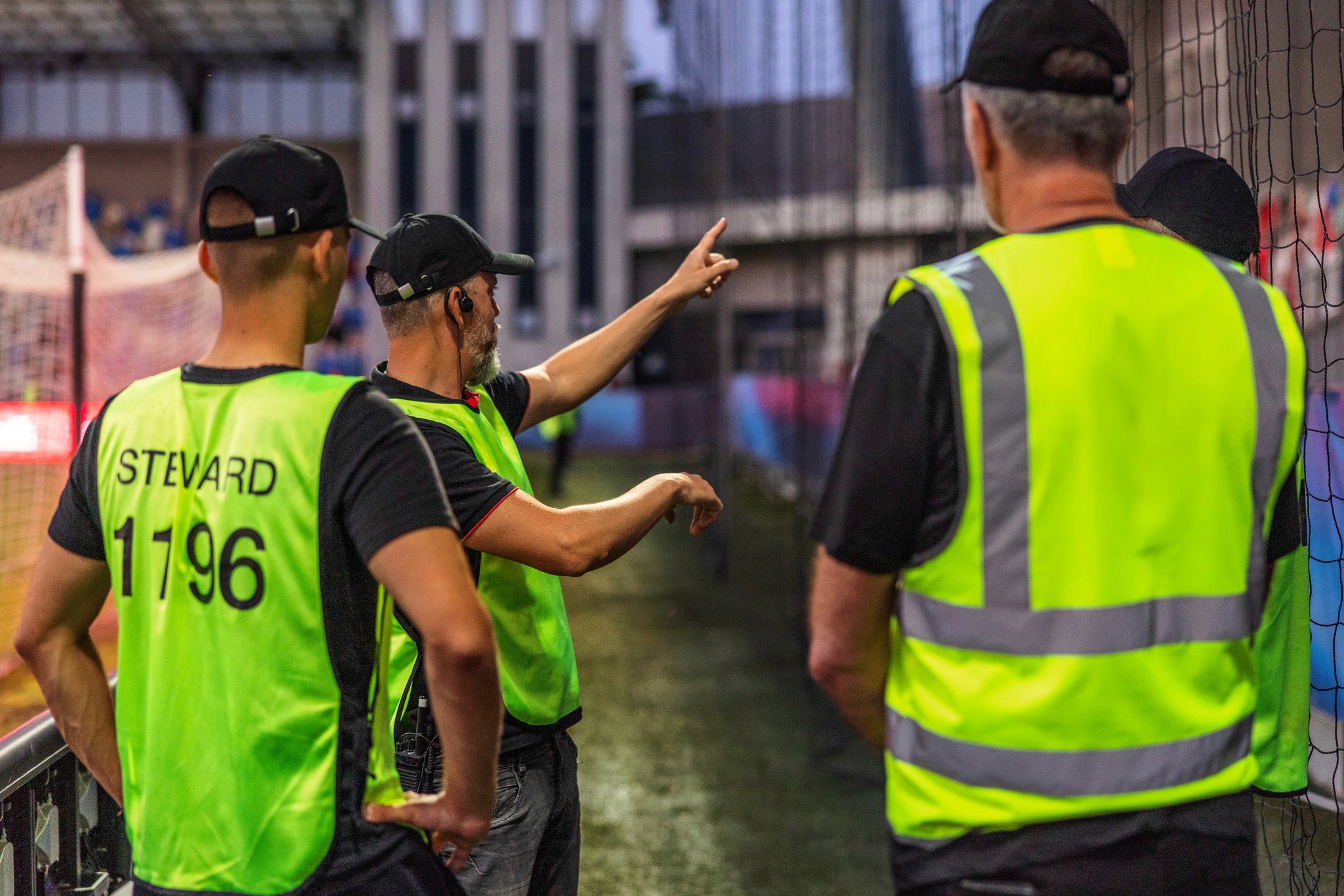
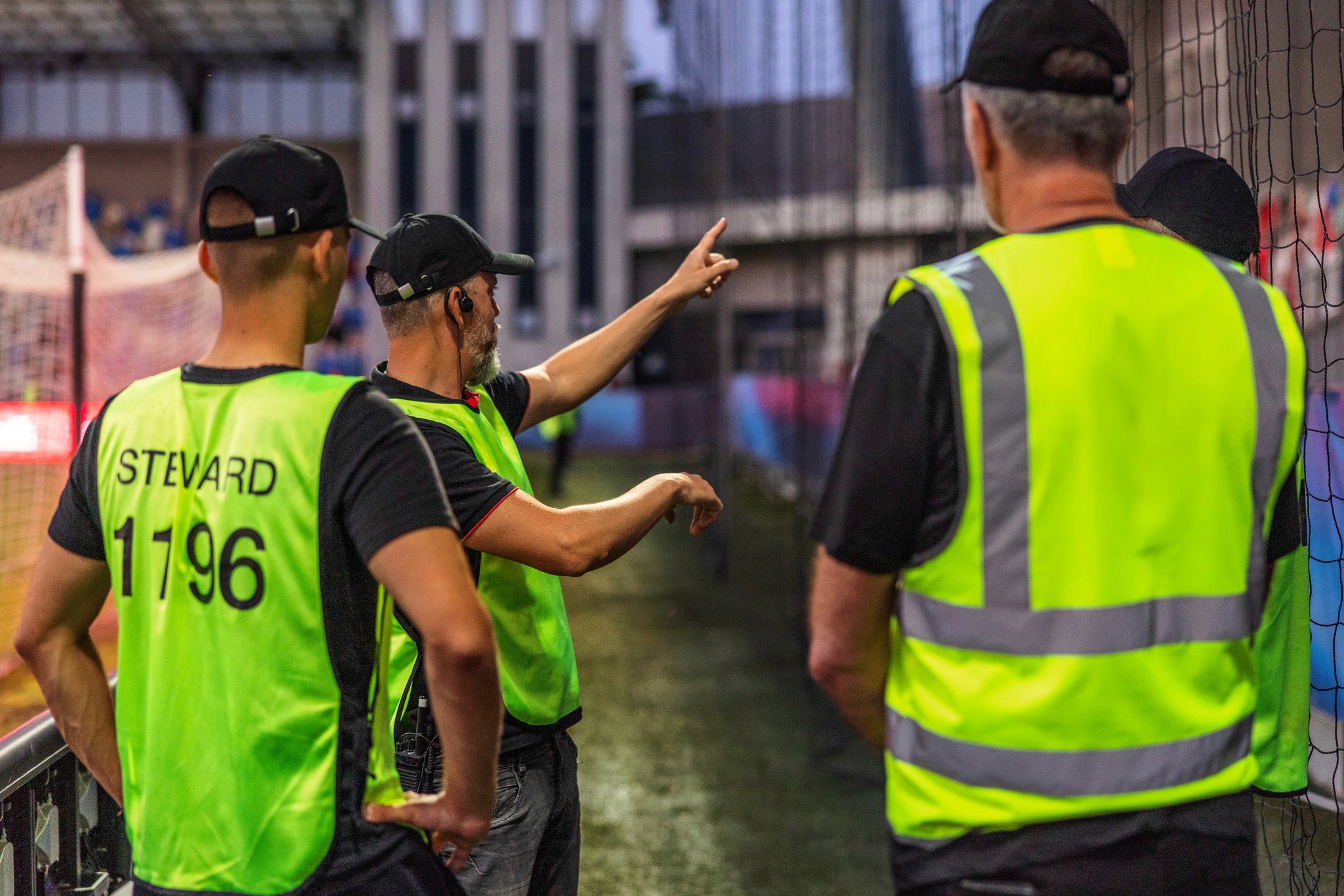
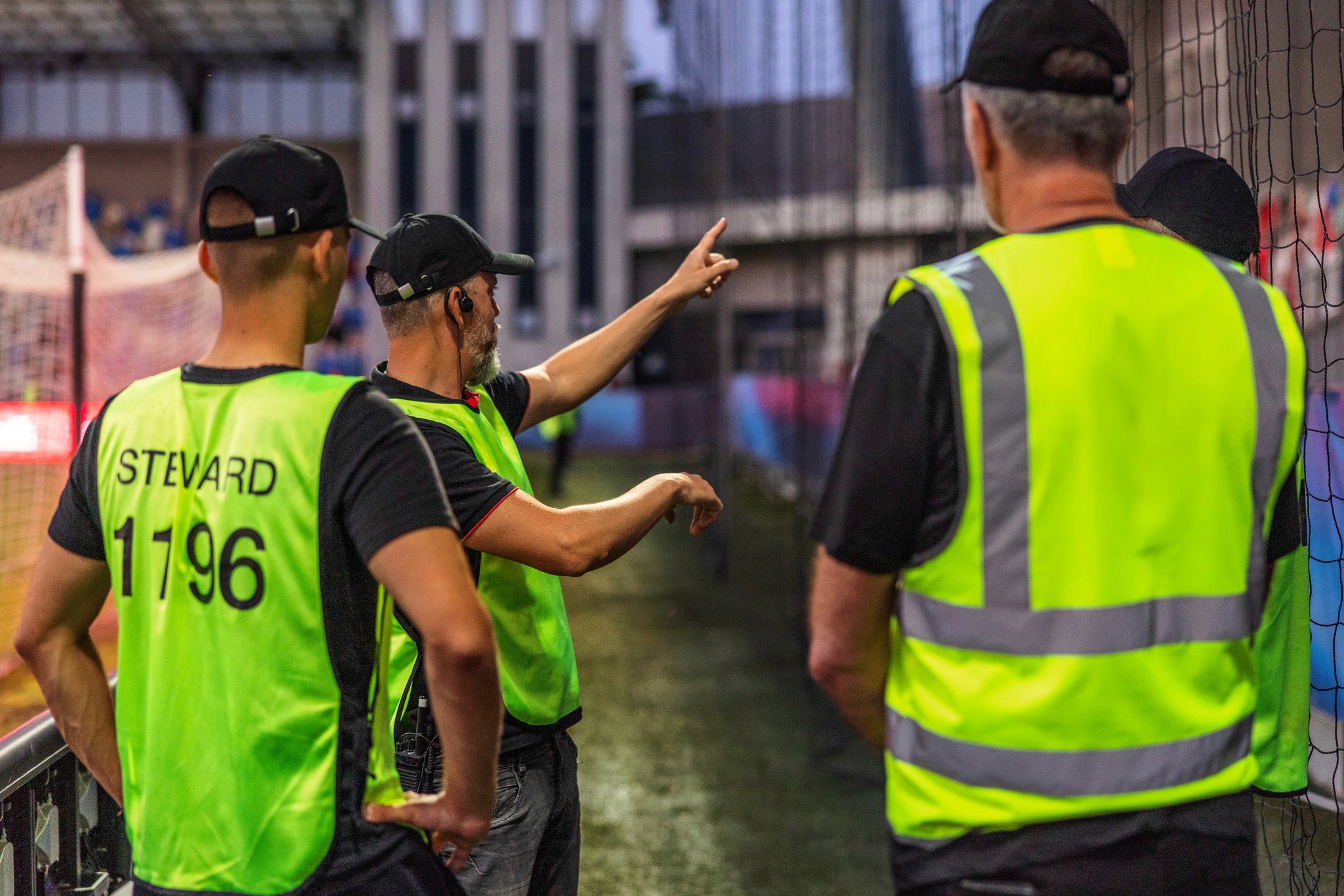
Events
Events
Events
Events
Delivering Reliable Staffing for a High-Volume Sports Events in the Southeast
Delivering Reliable Staffing for a High-Volume Sports Events in the Southeast
Delivering Reliable Staffing for a High-Volume Sports Events in the Southeast
Our client, a leader in event security and crowd management, supports several of the Southeast’s most prominent sports and entertainment venues, including a high-profile partnership with the NBA’s Miami Heat. After the pandemic, they faced the challenge of quickly re-establishing a reliable workforce to meet the increasing staffing demands of high-stakes events.
Talk to us about how Traba can improve your labor management.
chevron_left
Back to all case studies
How Traba Enhanced Workforce Quality and Efficiency for a Family-Owned Cosmetics Manufacturer
Aug 8, 2024
Manufacturing

99.6%
Average Shift Fill Rate
90%
Slots Filled by Returning Workers
83%
Slots Filled Within 24 Hours of Shift Start
Introduction
Location: Austin, TX
Industry: Cosmetics Manufacturing
Roles: Production operators such as; packers, general labor and machine operators.
Our client is a family-owned business that specializes in producing organic and natural cosmetic products. Quality and precision are paramount to them, as they cater to clients who expect their orders to be meticulously fulfilled according to exact specifications. Their demand remains relatively steady throughout the year, with a peak during the summer months.
Our client prides themselves on long-standing relationships with their partners, largely attributed to their unwavering commitment to quality.
Problem
Previous staffing solutions failed to meet Good Manufacturing Practice (GMP) standards and communication needs of the business.
Our client faced significant challenges with their previous staffing agency. Workers often arrived unprepared for GMP requirements, such as having long nails or wearing wigs, which compromised product quality and safety. Additionally, there was a lack of clear role matching and poor communication between the business and their prior traditional staffing agency, resulting in unresolved issues and operational inefficiencies.
Before partnering with Traba, our client struggled with inconsistent labor quality and unreliable staffing solutions, particularly during their peak season. Their product quality suffered and they were at risk of losing customers. Their defect rate started to increase as their quality assurance team started to notice smeared labels. They needed a dependable workforce that could maintain high standards and effectively manage the increased demand.
Solution
Traba provided our client with a roster of pre-vetted, high-quality workers who were well-prepared to meet GMP standards and other operational requirements. On average, it takes our client 26 minutes to see their first sign up on shifts, with 83% of positions being filled 24 hours in advance of the shift start time.
Workers were required to complete GMP training and certification prior to accepting any roles. By utilizing Traba's console, our client could create customized rosters featuring their favorite workers, ensuring a consistent and reliable team. The block feature in Traba's system allowed the business to curate an ideal workforce that aligned with their specific needs, with 90% of their slots being filled by returning workers.
Results
Since partnering with Traba, our client has experienced significant improvements in workforce quality and operational efficiency. Traba was able to achieve a 99.6% fill rate across roles. (Fill rate is calculated using the number of workers that completed shifts divided by the number of workers initially requested.) Their defect rate and return rates have decreased. Traba's understanding of the cosmetic manufacturing industry and proactive approach has provided consistent and high-performing labor which allowed the business to meet their production targets without fail. The majority of their workers are sourced solely from Traba, especially during their peak season. Clear communication and support have been crucial in addressing issues promptly and maintaining smooth operations.
The ease-of-use of Traba's business portal enabled quick adoption for all members of their team. This has empowered our client to manage the day-to-day of their family-run facility effectively, leading to increased volume output and operational scalability. As their production lines expanded, Traba scaled with them, providing the necessary resources to support their growth.
Now, early discussions are underway about acquiring another facility, highlighting the potential for further business growth when partnering with Traba.
Read more success stories like this
Talk to us about how Traba can improve your labor management.

Empowering businesses and workers to reach their full productivity and potential.
Copyright © 2025. All Rights Reserved by Traba

Empowering businesses and workers to reach their full productivity and potential.
Copyright © 2025. All Rights Reserved by Traba

Empowering businesses and workers to reach their full productivity and potential.
Copyright © 2025. All Rights Reserved by Traba

Empowering businesses and workers to reach their full productivity and potential.
Copyright © 2025. All Rights Reserved by Traba
chevron_left
Back to all case studies
How Traba Enhanced Workforce Quality and Efficiency for a Family-Owned Cosmetics Manufacturer
Aug 8, 2024
Manufacturing


chevron_left
Back to all case studies
How Traba Enhanced Workforce Quality and Efficiency for a Family-Owned Cosmetics Manufacturer
Aug 8, 2024
Manufacturing


chevron_left
Back to all case studies
How Traba Enhanced Workforce Quality and Efficiency for a Family-Owned Cosmetics Manufacturer
Aug 8, 2024
Manufacturing

